Agri Hour
Israeli technologies could boost SA agriculture─── 05:00 Mon, 18 Jan 2021
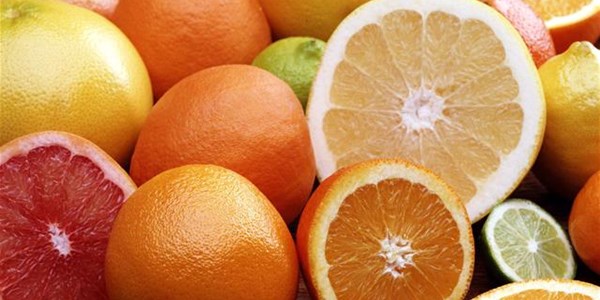
The trade office of the Israeli embassy in South Africa, together with the Fresh Produce Marketing Association’s South Africa office, jointly hosted the Virtual Agritech Roadshow to South Africa 2020.
OFM News's Elsabé Richard reports this webinar showcased several new Israeli-developed agricultural technologies.
Here is Elsabé...
See PODCAST below
While the global agriculture sector must produce significantly more food and fibre for the world’s rapidly growing population, there is great concern that the food value chain currently wastes about 1,3 billion tons of the food produced every year.
This is not only extremely counterproductive to achieving production targets but according to the 2018 US ‘Food waste investment report’, it loses the international food value chain around US$3 trillion (about R51 trillion) in potential profits and unnecessarily wastes or pollutes the planet’s already scarce natural resources.
A 2017 report by the World Wide Fund for Nature South Africa revealed that this country’s food value chain wasted about 10 million tons of food annually.
“Of this, fruit, vegetables and cereals account for 70% of the wastage and loss, primarily throughout the food supply chain, from farm to fork. The Council for Scientific and Industrial Research has valued this loss at R61,5 billion,” the report stated.
The water used to produce this wasted food would fill more than 600 000 Olympic-sized swimming pools.
Minimising food wastage
In 2017, having become keenly aware of the food waste crisis, Israel-headquartered company Trellis began working closely with international food and beverage producers to help predict their sourcing requirements from growers and accurately manage their supply chain operation.
“Our company has developed a data/artificial intelligence (AI) platform that can measure procurement and logistic inefficiencies, such as the timing of harvest, field-level yield and quality insights, all the way to the optimal freight and production plan,” says Ilay Englard, co-founder and CEO of Trellis.
“The ability to leverage field-level data for downstream production is leading a new category of autonomous food supply chains that will significantly reduce waste and food costs and, at the same time, preserve global resources.”
Managing food supply
Englard explains that Trellis’s AI technology uses agricultural technology data in combination with operational and business data to help decision-makers better plan and manage food supply and demand along the “extremely complex” chain from field to final product.
Accessible on any smartphone, tablet, laptop or computer, Trellis’s technology provides improvements in efficiency at key stages across the food supply chain.
“Our AI has studied decades of historical harvest data, and continues to examine the production of the world’s largest food systems, as well as ongoing market and weather trends,” the company states.
“By analysing large and complex agri-food supply chain data, and identifying often well-hidden patterns in biological and atmospheric factors, Trellis develops in-house algorithms and modules designed to offer food and beverage companies comprehensive insights.
“The algorithms process over five million data points daily, generating real-time actionable insights.”
Englard adds that, to date, Trellis’s AI technology has optimised over 10 000 data blocks in the global food supply chain in which Trellis operates, and analysed over 50 000 harvests of various crops.
Quality control
As many of the world’s fresh produce growers will agree, the prices that they receive on the market floor are often largely based on the buyers’ subjective assessments of the quality of the produce.
In these cases, where the produce has already been transported from the farm to the market, the sellers usually have few options other than to accept a buyer’s price, or reject it and risk the produce losing quality as it stands over to the next day.
Elad Mardix, president of Clarifruit, an on-the-go automatic quality control and data analytics platform for fresh produce, says that of the approximately 400 million transactions that take place annually on fresh produce market floors globally, 20% have their prices renegotiated the following day, and in 5% of cases, the fresh produce is totally rejected.
This results in an average 6,5% loss in profit for the world’s fresh produce sellers. The average profit margin for players in the global fresh produce supply chain is only 3% to 5%.
“Although the global fresh produce industry invests 0,5% to 1% of its revenue in managing its quality control, labour and systems, these processes have, until now, remained largely ineffective because they are slow, subjective, expensive, prone to error, and have enabled limited collaboration between players in the supply chain,” Mardix explains.
The Clarifruit automatic quality control and data analytics platform aim to resolve many of these problems. Clarifruit comprises a combination of three software applications, which the company has named the Inspector (a front-end smartphone app); the Quality Control Manager (a laptop or desktop computer app); and the Operations Director (a big data and analytics platform hosted by Clarifruit).
The Inspector smartphone app, which is compatible with iOS and Android, integrates with any enterprise resource management system and harnesses a smartphone’s existing camera technology to apply computer-vision technology.
Mardix explains that the Inspector enables a producer to photograph a sample fruit or vegetable and have its external characteristics analysed automatically for size, colour, stem colour, and defects.
Specialised third-party industry devices can be wirelessly integrated into the smartphone so that the Inspector can automatically analyse the internal characteristics of the sample, such as its Brix, firmness, and pH, among others.
The Inspector quickly generates a quality control assessment and instantly transmits the results to the business’s enterprise resource planning system.
Clarifruit’s Quality Control Manager app collects, analyses and manages (in real-time) the results from numerous linked smartphones using the Inspector, wherever these happen to be in the world. The Operations Director platform then harnesses all of these assessments to generate insights that can help the company make more profitable decisions, such as better matching product quality to customer specifications, thus helping to avoid rejections.
“Our Clarifruit platform can significantly improve a fresh produce business’s profitability, as it allows growers and packhouses to quickly sort sub-quality produce from marketable produce, resulting in fewer rejections by buyers on the market floor. And the ability of the Inspector to quickly and easily assess fruit and vegetable quality means that larger samples can be analysed. This gives a more accurate representation of the quality of the entire fresh produce consignment,” says Mardix.
Monitoring the cold chain
Yaron Nemet, co-founder and CEO of Varcode, which uses dynamic barcode technology to monitor the perishable foods cold chain from farm to fork, says that 32% (192 million) of the approximately 600 million annual global cases of food-borne illnesses are in some way linked to faults in the perishable foods cold chain.
He adds that, according to information published by the Food and Agriculture Organization of the United Nations, these faults are also the cause of 1,3 billion tons of food having to be discarded every year. As a solution to this, Varcode has developed technologies to create the company’s FreshCode barcoded tags that monitor and record temperatures throughout a perishable product’s journey along the cold chain.
“Varcode’s FreshCode tags are manufactured using a combination of precisely tuned chemicals and a unique printed layer to record temperature variations and the time and length of these. Each tag has a unique serial number and can be scanned anywhere by fixed and handheld standard barcode scanners and smartphones to immediately give a log of the temperatures that a FreshCode-tagged perishable product has been exposed to,” explains Nemet.
The tags and the related track-and-trace software can also generate real-time records of who scanned a tag, what perishable product was tagged, when and where it was scanned, and whether or not the tagged product was exposed to temperatures outside of set parameters. The software issues a warning for any such out-of-parameter incidents, enabling users to identify the reasons for the lapse and handle the affected products appropriately.
Nemet says that in addition to the enhanced food safety provided by FreshCode tags, the costs of purchasing and using these tags and their associated software and hardware are lower “by a huge margin” than any other perishable foods cold chain monitoring technology. According to him, purchasing and operating the FreshCode system can cost up to 90% less than similar competitive technologies. And deploying accurate temperature monitoring down to box level can result in further savings by extending a perishable product’s shelf life.
Email Trellis at info@trellis.ag, or visit trellis.ag.
Email Clarifruit at info@clarifruit.com, or visit clarifruit.com.
Email Varcode at info@varcode.com, or visit varcode.com.